By Jenny Kincaid Boone,
Joseph DeSimone believes there is a key to getting the battered economy back up and running in the midst of COVID-19 — design accurate tests for the virus and make plenty of them.
The Silicon Valley entrepreneur and accomplished Virginia Tech alumnus is co-founder and executive chairman of Carbon Inc., a digital manufacturing company that uses a rapid 3D printing technology called Digital Light Synthesis, to create products for some of the world’s major brands, from Johnson & Johnson to Adidas.
His Redwood City, California-based company took a proactive approach to a problem that emerged as a result of the pandemic’s spread — a shortage of nasopharyngeal or upper nasal cavity testing swabs. Production facilities for conventional swabs, including one in Italy located in a region hard hit by the pandemic and subject to early shutdowns, could not keep up with demand.
“To get the economy back and to do so with people’s health and safety as the top priority, you need to know who’s contagious and who’s not.”
- JOSEPH DESIMONE
Carbon worked with Minneapolis-based Resolution Medical, a medical device company and one of the company’s production partners. The task was to design and create new testing swabs with a material typically used to make dental and orthodontic products, such as nightguards. With the dental market on hold at the height of the pandemic, there was capacity for Carbon’s dental lab partners to help with swab production.
For the swabs, which are 3D printed, the use of a soft plastic material that was already FDA approved expedited the product’s launch, said DeSimone, a chemist who founded Carbon in 2013.
“This is a medical device that needs to have a lot of performance characteristics,” said DeSimone, who earned a Ph.D. in chemistry at Virginia Tech in 1990, studying with his mentor, the late Professor James McGrath. “It needs to be safe, it needs to be effective, it needs to be as comfortable as it can be, and it needs to collect the mucus and the biological specimen efficiently.”
The flexible swabs have a spiral stem, wrapped with a lattice that was designed using Carbon’s lattice generation software created by Hardik Kabaria, software engineering manager for the company. They were clinically tested at Stanford Health Care and Beth Israel Deaconess Medical Center in Boston.
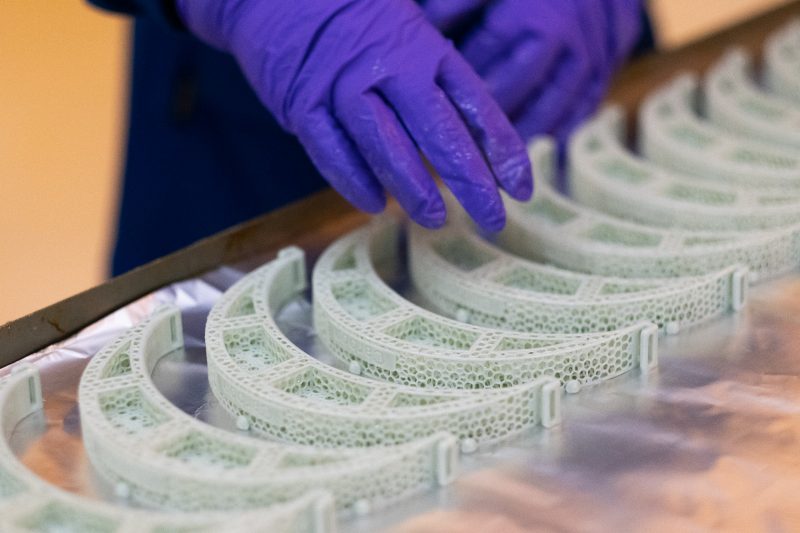
Three weeks after the initial design was made, Resolution Medical began selling and distributing the swabs to healthcare facilities nationwide. The first weekly shipments in April totaled about 10,000, and as of late June, more than a half million swabs have been shipped to hospitals around the country, DeSimone said.
“The capacity is there to produce up to a million swabs per week, and dependent on need, this could increase to multiple millions per week,” he said.
Compared with the standard testing swabs, these new models show early indication of being more accurate in detecting COVID-19, DeSimone said. The potential to improve the false negative rate is “profoundly impactful,” he said. “To get the economy back and to do so with people’s health and safety as the top priority, you need to know who’s contagious and who’s not.”
“It’s really fascinating to see a whole new market emerge around testing for improved performance to help allow the economy to get back up and running,” added DeSimone, who is one of only 25 people nationwide elected to all three branches of the National Academies. Carbon also transformed its research and development facility in Santa Clara, California, into a manufacturing location for face shields. As of July, the company and its network of dental partners produced more than 350,000 face shields for healthcare and essential workers using either a dental resin or a polyurethane material typically found in the midsole of an Adidas shoe.
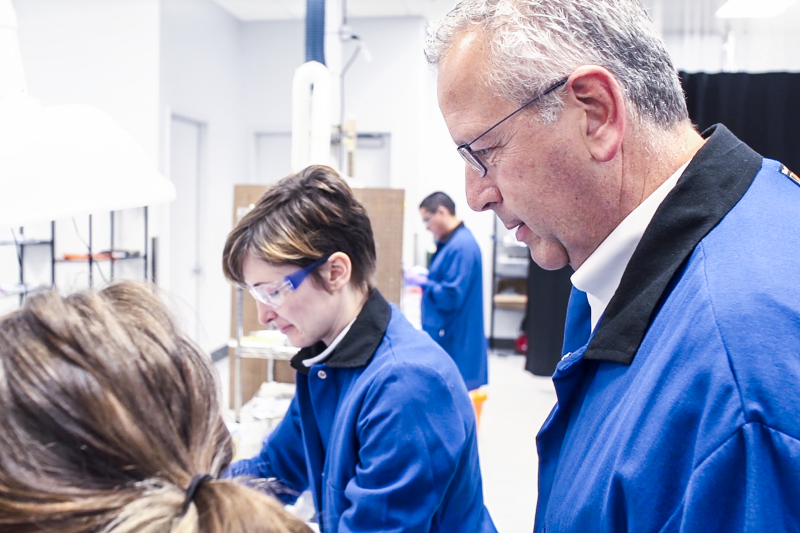
The shields have landed in hospitals throughout the country, including in New York, Washington, and Seattle. DeSimone personally delivered them to some local restaurants and grocery stores.
For his frequent visits to the company’s manufacturing facility during California’s stay-at-home orders, DeSimone carried a letter from Carbon’s general counsel explaining the company’s work in the COVID-19 effort as an authorization to venture outside of his home.
Now, some of Carbon’s operations are returning to pre-pandemic levels, but many unknowns remain, DeSimone said. He believes the world has changed as a result of COVID-19. “This is going to be like 9/11 in that it is a new world,” he added. “It will take us three or four years to figure out.”
For an expanded story on Joseph DeSimone and his work with Virginia Tech’s Innovation campus, visit Entrepreneurial alumnus leads design of pandemic-fighting tools.